|
|
Product Show
Product name : Inconel 625
Item :Nickel Alloy
Price :
Details :
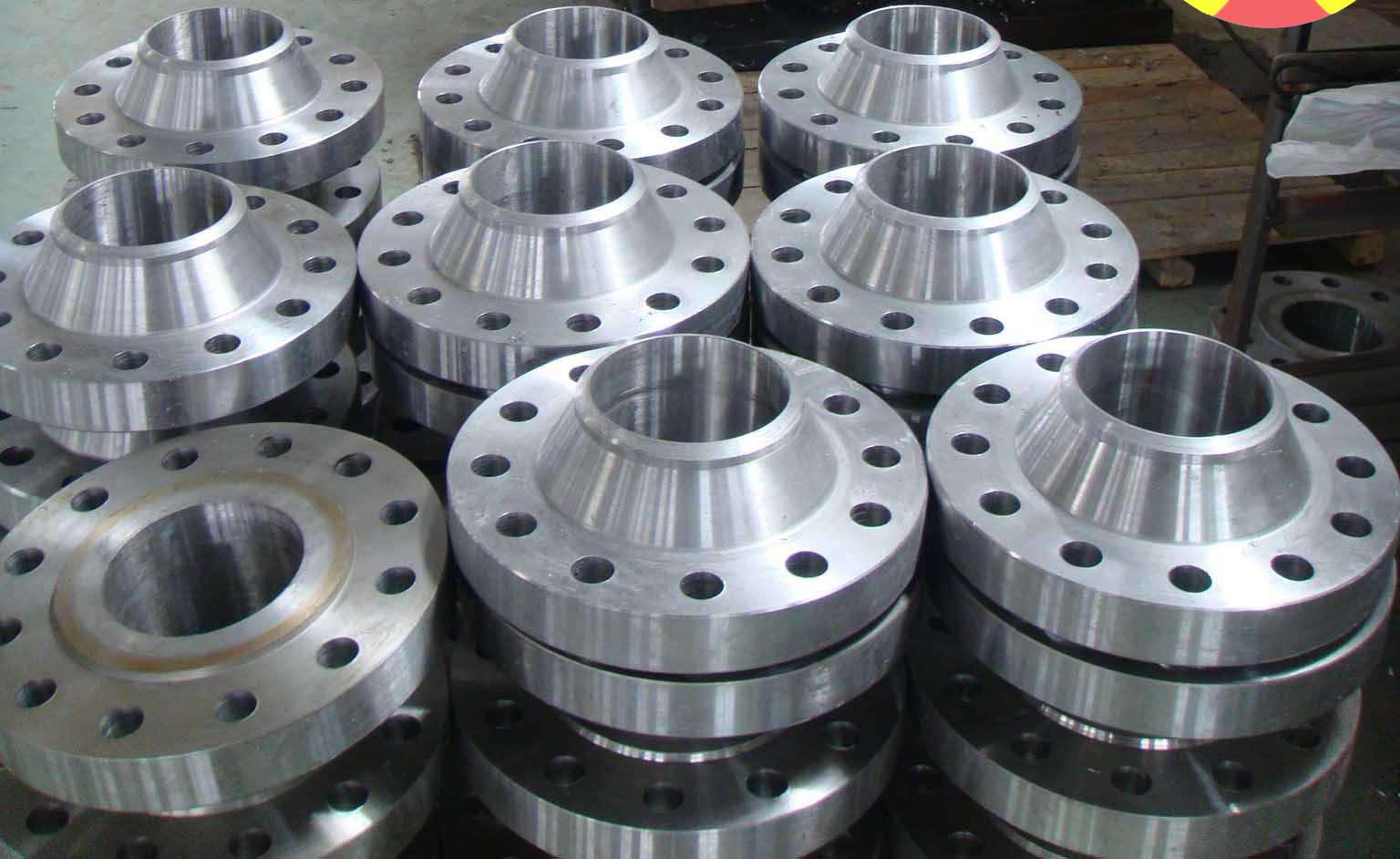
Nickel alloy 625 has been utilised for its high strength and outstanding corrosion resistance.
The strength of alloy 625 comes from the effects of molybdenum and columbian.
Alloy 625 is also used for it’s superb weldability and has been often used to weld AL-6XN® alloy.
Alloy 625 is also referred to as Inconel® 625, Alloy 625, Nickel 625 and is available in 625 Sheet, 625 Welding Products, 625 Bar and 625 Plate.
- Fully certified and backed up by our in-house NDT/NDE Inspectors & Metallurgists
- Available as Bar, Billet, Forgings and Machined Components
Chemical composition
% |
Ni |
Cr |
Mo |
Fe |
C |
Mn |
Si |
P |
S |
Co |
Nb+Ta |
Al |
Ti |
min |
58.0 |
20.0 |
8.0 |
|
|
|
|
|
|
|
3.15 |
|
|
max |
|
23.0 |
10.0 |
5.0 |
0.10 |
0.50 |
0.50 |
0.015 |
0.015 |
1.00 |
4.15 |
0.40 |
0.40 |
Specification Sheet: Alloy 625 (UNS N06625) W. Nr. 2.4856
An Austenitic Nickel-Chromium-Molybdenum-Niobium Alloy with Outstanding Corrosion Resistance and
High Strength from Cryogenic Temperatures to 1800°F (982°C)
Standards: ASTM B443, ASME SB 443, AMS 5666
Description
Alloy 625 is an austenitic nickel-chromium-molybdenum-niobium alloy possessing a rare combination of outstanding corrosion resistance coupled with
high strength from cryogenic temperatures to 1800°F (982°C).
The strength of Alloy 625 is derived from the solid-solution hardening of the nickel-chromium matrix by the presence of molybdenum and niobium. Therefore,
precipitation-hardening treatments are not required.
The chemical composition of Alloy 625 is also responsible for its outstanding corrosion resistance in a variety of severe operating environments along with
resistance to oxidation and carburization in high temperature service.
The alloy is resistant to pitting, crevice corrosion, impingement corrosion, intergranular attack and is almost immune to chloride stress corrosion cracking.
Alloy 625 can be easily welded and processed by standard shop fabrication practices.
Oxidation Resistance
The oxidation and scaling resistance of Alloy 625 is superior to a number of heat resistant austenitic stainless steels such as 304, 309, 310 and 347 up to
1800°F (982°C) and under cyclic heating and cooling conditions. Above 1800°F (982°C), scaling can become a restrictive factor inservice.
Applications
- Aerospace Components — bellows and expansion joints, ducting systems, jet engine exhaust systems, engine thrust-reversers, turbine shroud rings
- Air Pollution Control — chimney liners, dampers, flue gas desulfurization (FGD) components
- Chemical Processing — equipment handling both oxidizing and reducing acids, super-phosphoric acid production
- Marine Service — steam line bellows, Navy ship exhaust systems, submarine auxiliary propulsion systems
- Nuclear Industry — reactor core and control rod components, waste reprocessing equipment
- Offshore Oil and Gas Production — waste flare gas stacks, piping systems, riser sheathing, sour gas piping and tubing
- Petroleum Refining — waste flare gas stacks
- Waste Treatment — waste incineration components
Physical Properties
Density 0.305 lbs / in3 8.44 g /cm3
Modulus of Elasticity 30.1 x 106 psi 207.5 GPa
Melting Range 2350 – 2460°F 1290 – 1350°C
Specific Heat 0.102 BTU/lb-°F (32 – 212°F) 427 J/kg-°C (0 –100°C)
Thermal Conductivity 212°F (100°C) 75 BTU-in/ ft2-h-°F 10.8 W/m-°C
Electrical Resistivity 50.8 Microhm-in at 70°F 128.9 Microhm-cm at 21°C
Mechanical Properties
Typical Values at 68°F (20°C)
Yield Strength .2% Offset – PSI 60,000 (Mpa) 414
Ultimate Tensile Strength – PSI 120,000 (Mpa) 828
Elongation in 2in – 50%
Hardness – 200 Brinell
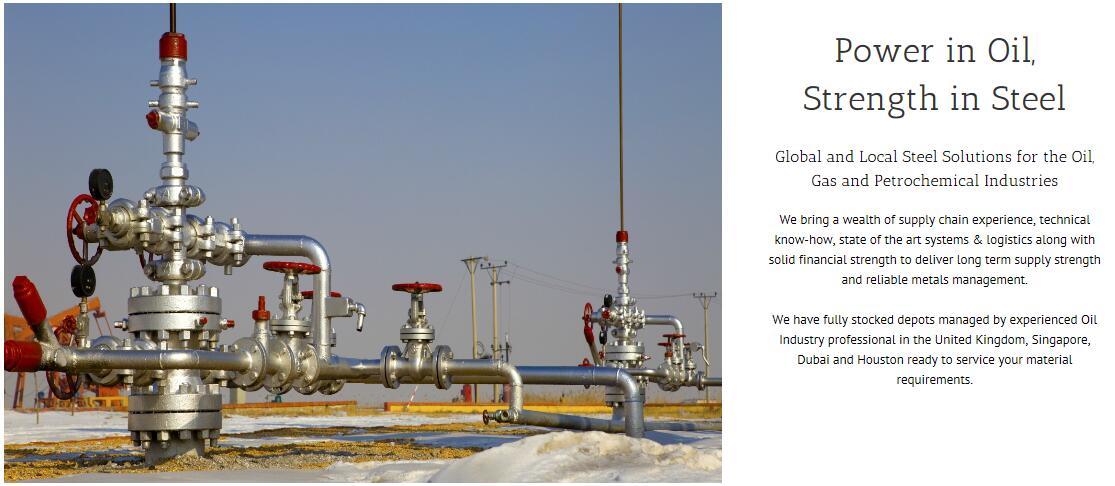
|