Product focus – Nickel Foil
When an ultra-thin material is required, nickel foil offers exceptional thinness without sacrificing its corrosion resistance or strength
In so many industries, precision is key when it comes to selecting materials to manufacture important and essential parts. Tolerances are small and every micrometre counts, but there are limitations to how thinly metal alloys can be produced by traditional cold-rolling methods. This is why nickel foil is a key product for many design engineers, as it fills a niche gap in the market and enables the development of new and innovative components.
Nickel foil is exceptionally thin; it comes in a range of thickness from 6μm to 150μm. Conventional rolling techniques for metal alloys can’t get close to this thinness and remain economically viable, which means that newer, state-of-the-art methods need to be employed.
The nickel foil that Corrotherm offers is made from high-purity nickel (over 99.97% nickel) and it is electro-deposited, which means that it can be produced more thinly and also in greater widths (up to 1,020mm) than previously possible.
This needs to be done by skilled manufacturers using cutting-edge techniques, but it also requires engineers producing the product to have practical, hands-on knowledge to achieve exceptional-quality results with years of experience in the industry. It’s therefore important to work only with trusted suppliers and manufacturers to ensure that the nickel foil meets the high expectations and requirements of customers.
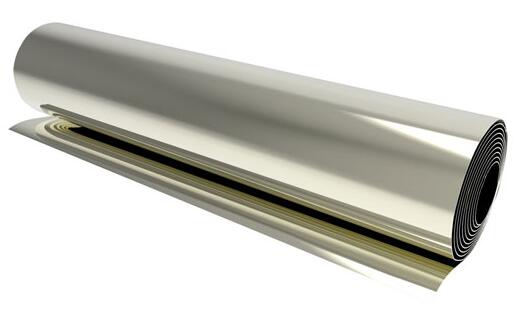
Product specifications
As well as a range of different thicknesses, the nickel foil product can also have a choice of surface finishes, which offers versatility and flexibility for material selection. The finish can either be of optical-quality mirror standard, or more textured – the roughness is entirely customisable. There are also options to add adhesive coatings, lamination (on one side or both), black nickel oxide coating or PTFE impregnation.
However it is manufactured and to whatever specifications, the nickel foil retains some impressive properties. For example, it maintains the corrosion resistance of the nickel, as well as good performance in hot operating temperatures. It has a tensile strength of up to 790MPa in its raw electro-deposited state and up to 300MPa when fully annealed. It also has good welding and forming capabilities, and high magnetic properties, inherent to the nickel, which makes it useful in certain applications.
Applications
So where would nickel foil be used? There are many different industries that can make use of such a specific product. It has a lot of engineering applications, such as in gaskets, battery mesh, fuel cells, heating elements, pressure valve bursting discs, lead frames, printed resistor/circuit boards, electronics, micro-electronics, electrical, EMI, RFI, power storage, polymer fuses, process substrates, medical, analytical, aerospace, automotive, dental, renewable energy, RFID, security tags and heat treatment. To find out more about this product and the different finishes, treatments and sizes available