INCONEL alloy 601, a super-alloy that shows exceptional high-temperature resistance and strength, which makes it useful for the extreme environments in many industries.
INCONEL alloy 601 is a powerful and technical material that is used across a wide range of industries, particularly in extreme environments where precision and stability are incredibly important.
For example, it is a key component used in jet engines and across the aerospace industry as a whole. While it is quite broadly used in this sector, applications include combustion-can liners, containment rings in gas turbines (for aircraft, vehicles and industrial applications), diffuser assembles and jet-engine igniters.
It also plays an important role in many processing situations, including chemical, petrochemical, waste and thermal. It is a fairly standard material in the thermal-processing arena for things like baskets, trays, heat-treating operations, radiant tubes, muffles, flame shields, chain curtains, burner nozzles… the list goes on. It is a material that is commonly found in thermal reactors in the exhaust system of petrol engines. When it comes to chemical-processing, it is useful for condenser tubes in sour-water strippers and insulating cans in ammonia reformers, as well as combustor components.
INCONEL alloy 601 is found within the power-generation industry, where it can be used for ash-handling systems, grid barriers and superheater tube supporters. It has a few more creative applications too. For example, it is widely used as thermowell sheathing material and oxygen injection tubes in the metal and glass-making industries, as well as in the form of tubing for ceramic tile production for modern roller hearth ovens.
Key properties
As you can see, INCONEL alloy 601 is quite ubiquitous in various kinds of industrial sectors, and its popularity as a general-use material is not waning. The reason that it is a material of choice by engineers across all of these sectors is because of its exceptional properties and characteristics. It exhibits particularly good resistance to high-temperature oxidation up to around 1,250°C. This is true even in more severe conditions, such as cyclical heating and cooling, where the alloy’s tightly adherent oxide layer resists spalling. It also has good resistance to carburisation, in carbon-nitriding conditions, against aqueous corrosion, and in oxidising sulphur-bearing atmospheres.
It also has a high mechanical strength. It is a versatile material that can be readily formed, machined and welded for a broad range of uses. It is best machined in solution-treated condition, and all standard machining and welding procedures can be applied.
Composition
It is the precise blend of elements within the alloy that give it these valuable properties. Its nickel and chromium base is what gives the material such good resistance in high-temperature conditions and against many corrosive media. The chromium content is high, around 21-25%, to help impart these characteristics. The addition of a small amount of aluminium also enhances the material’s resistance against oxidisation.
When exposed to high temperatures, these three elements work together to form an extremely protective and adherent oxide film across the surface of the alloy. Some internal oxidation does occur, which provides a higher chromium content in the surface oxide. This gives the material its unique corrosion resistance properties.
Find out more about INCONEL alloy 601, please contact a member of our sales expert.
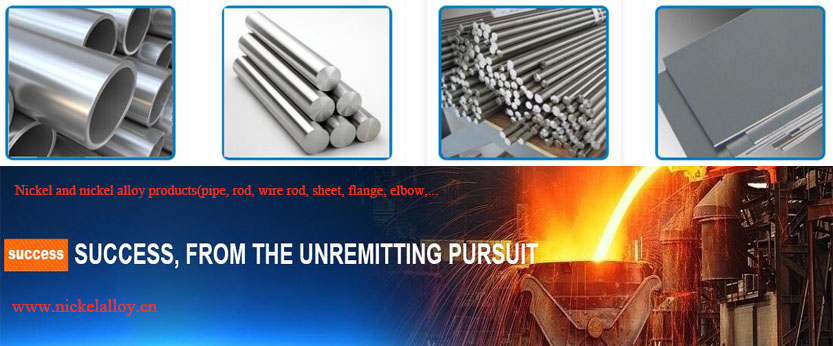